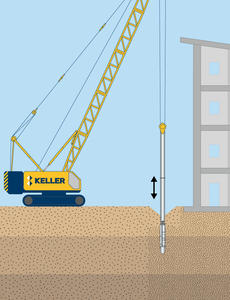
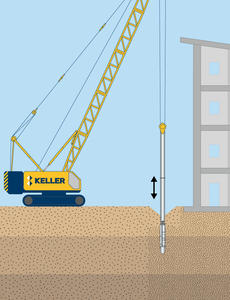
Wzmacnianie podłoża
Celem wzmacniania podłoża jest zwiększenie jego nośności, zmniejszenie osiadania oraz poprawa właściwości fizycznych gruntu. Proces polega na modyfikacji właściwości gruntu lub wykonaniu inkluzji w celu osiągnięcia wymaganej wytrzymałości.

Fundamenty głębokie
Fundamenty głębokie są optymalnym rozwiązaniem w przypadku konieczności przeniesienia obciążenia na nośne podłoże przez wyżej zalegające grunty nienośne lub słabonośne. Ich zastosowanie polega na wykonaniu głębokich elementów konstrukcyjnych przenoszących obciążenie na nośne podłoże.
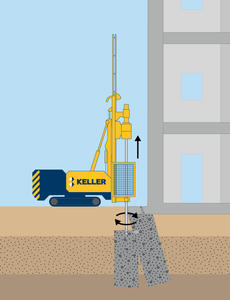
Technologie iniekcyjne
Technologie iniekcyjne wykorzystuje się do wzmacniania podłoża oraz kontroli przepływu wód gruntowych poprzez zmniejszenie przepuszczalności gruntów. Można je stosować do realizacji nowych projektów budowlanych oraz w pracach naprawczych i konserwacyjnych istniejących obiektów.
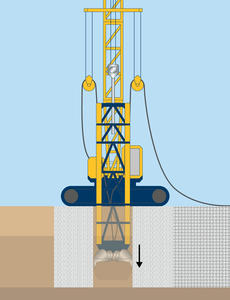
Zabezpieczenie wykopów, skarp i zboczy
Zabezpieczenie wykopów, skarp i zboczy obejmuje systemy obudów i stabilizacji w ramach jednej bądź kilku technologii. Mogą być stosowane do stabilizacji naturalnych niestabilnych zboczy, zabezpieczenia wykopów fundamentowych lub wsparcia sąsiadujących konstrukcji.
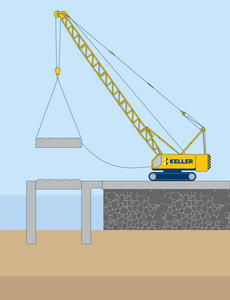
Konstrukcje hydrotechniczne