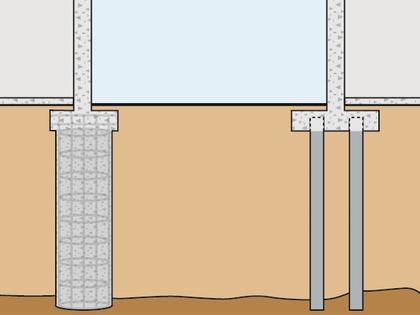
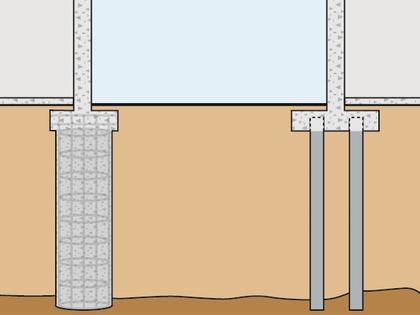
Zwiększanie nośności
Przekazanie obciążenia na głębsze warstwy nośnego podłoża.
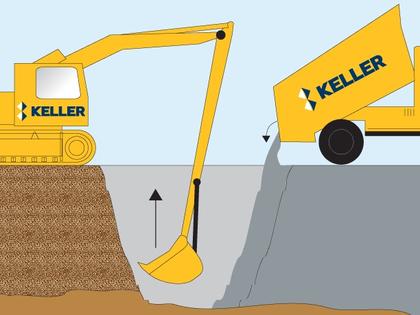
Bariery uszczelniające lub odcinające
Zatrzymanie migracji zanieczyszczeń w gruncie lub zapobieganie przesiąkania wody przez zaporę lub wał.
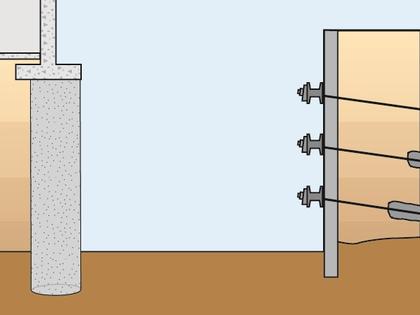
Zabezpieczenia wykopów
Wykonanie stabilnych wykopów, zapobieganie ruchom i uszkodzeniom konstrukcji i instalacji.

Konstrukcje hydrotechniczne
Usługi dla rynku budownictwa wodnego.
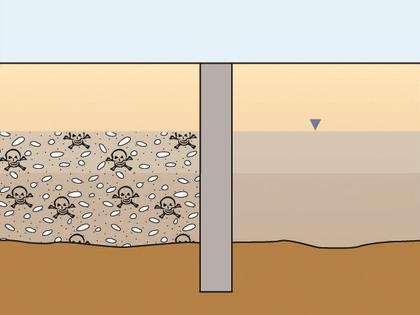
Remediacja i rekultywacja
Remediacja wód podziemnych i gruntów w celu redukcji zanieczyszczeń.
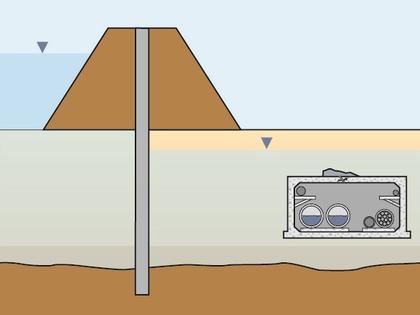
Przesłony i uszczelnienia przeciwfiltracyjne
Kontrolowanie lub zapobieganie filtracji wody.
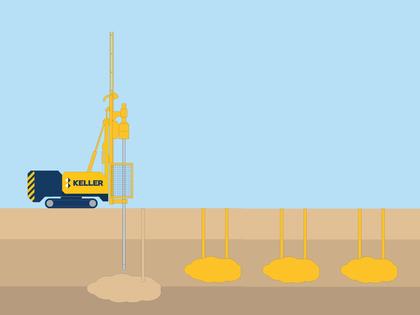
Stabilizacja
Szereg rozwiązań wzmacniających niestabilne podłoże.
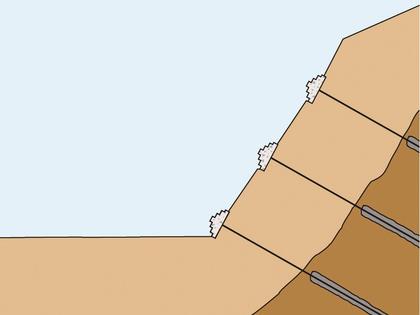
Zabezpieczenie skarp i zboczy